Service Factory Automation
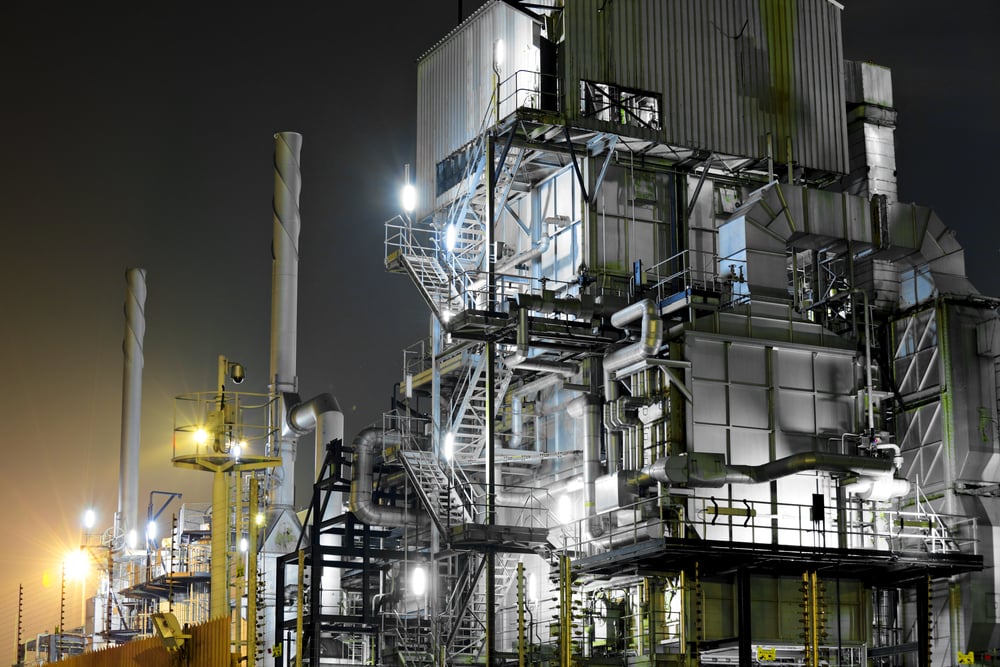
Factory Automation
The decision on how to embark on or expand a smart factory initiative should align with the specific needs of an organization. Undertaking a smart factory journey generally addresses categories as asset efficiency, quality, costs, safety, and sustainability.
Considering the possibilities, starting small with manageable components, and scaling quickly to grow the operations, the promise and benefits of the smart factory can be realized.
The smart factory represents a leap forward from more traditional automation to a fully connected and flexible system A true smart factory can integrate data from system-wide physical, operational, and human assets to drive manufacturing, maintenance, inventory tracking, digitization of operations through the digital twin, and other types of activities across the entire manufacturing network. The result can be a more efficient and agile system, less production downtime, and a greater ability to predict and adjust to changes in the facility. True smart factory is a more holistic endeavor, moving beyond the shop floor toward influencing the enterprise and broader ecosystem.
1. Our expertise is to identify the key features, and the trends that have contributed to manufacturing improvements.
2. The components and technologies that comprise the smart factory, and how it fits within the digital supply network.
3. How the smart factory can drive value and its other benefits .
4. Ways organizations can begin building and enacting a true, holistic smart factory.
5. Data can take many forms and serve many purposes within the smart factory environment. The power of algorithmic analyses, data drive all processes, detect operational errors, provide user feedback, and, when gathered in enough scale and scope, can be used to predict operational and asset inefficiencies and fluctuations.
For a smart factory to function, all the data acquisition systems need to be leveraged. These include Control System – such as PLC, SCADA, MES etc. and along with these data acquisition systems organizations will need to consider other technologies as well, including transaction and enterprise resource planning systems, IoT and analytics platforms, and requirements for edge processing and cloud storage, among others. This could require implementing the various digital and physical technologies inherent in Industry 4.0—including analytics, additive manufacturing, robotics, high-performance computing, AI and cognitive technologies, to connect assets and facilities, make sense of data, and digitize business operations